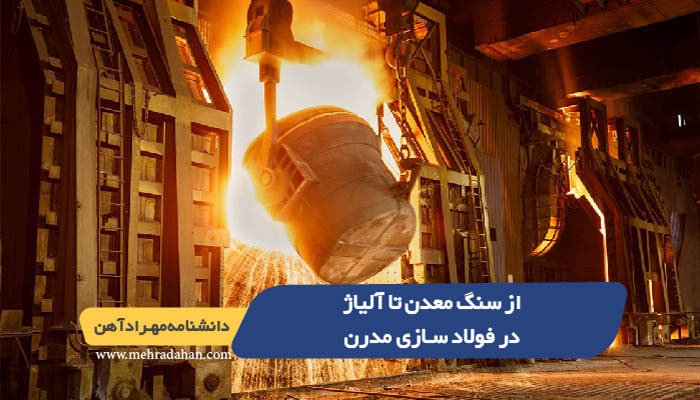
از سنگ معدن تا آلیاژ در فولاد سازی مدرن
فولاد یک ماده اساسی در صنعت مدرن است که برای ساخت و ساز، تولید، حمل و نقل و کاربردهای بیشماری دیگر ضروری است. در قلب تولید فولاد، فرآیند پیچیده ساخت آهن نهفته است، جایی که سنگ آهن به آهن مذاب تبدیل می شود و در نهایت آلیاژ می شود تا درجات مختلف فولاد ایجاد شود. این دانشنامه به سفر از سنگ معدن تا آلیاژ در فولاد سازی مدرن می پردازد و فناوری ها، چالش ها و نوآوری هایی را که فولاد سازی مدرن را شکل می دهند، بررسی می کند.
۱. سنگ آهن: منبع استحکام فولاد
سنگ آهن، در درجه اول هماتیت و مگنتیت، به عنوان ماده خام برای ساخت آهن عمل می کند. معادن در سرتاسر جهان این سنگها را استخراج میکنند و سپس برای حذف ناخالصیها و افزایش محتوای آهن پردازش میشوند. تکنیکهای غنیسازی پیشرفته مانند جداسازی مغناطیسی و شناورسازی کف تضمین میکند که سنگ آهن با عیار بالا وارد فرآیند فولاد سازی میشود و کارایی و کیفیت محصول را بهینه میکند.
۲. کوره بلند: نوآوری باستانی، کاربرد مدرن
کوره بلند نمادی از فولاد سازی سنتی است که قدمت آن به قرنها پیش میرسد. در این فرآیند، سنگ آهن، کک (شکلی از کربن) و سنگ آهک وارد کوره می شوند، جایی که گرمای شدید و واکنش های شیمیایی آهن مذاب را استخراج می کنند. نوآوریها در فناوری کوره بلند، از جمله سیستمهای انفجار داغ، غنیسازی اکسیژن و مواد نسوز، بهرهوری و عملکرد زیستمحیطی را به طور قابلتوجهی بهبود بخشیده است.
۳. کاهش مستقیم: مسیرهای پیشگام به سوی آهن
فنآوریهای احیای مستقیم یک مسیر جایگزین برای فولاد سازی، دور زدن کوره بلند معمولی ارائه میدهند. فرآیندهایی مانند سیستمهای Midrex و HYL/Energiron از گاز طبیعی یا هیدروژن برای کاهش گلولهها یا کلوخههای سنگ آهن استفاده میکنند و آهن کاهش یافته مستقیم (DRI) یا آهن اسفنجی را تولید میکنند. این روش ها که به دلیل بهره وری انرژی و انتشار کمتر شناخته شده اند، نقش حیاتی در تولید فولاد مدرن، به ویژه در مناطقی با منابع گاز طبیعی فراوان دارند.
۴. کوره قوس الکتریکی (EAF): ذوب و اختلاط
کورههای قوس الکتریکی در کنار کورههای بلند و کارخانههای احیای مستقیم، نقش مهمی در فولادسازی دارند. ضایعات فلزی، DRI و سایر ورودی های فلزی در EAF با استفاده از قوس الکتریکی پرقدرت ذوب می شوند. این فرآیند نه تنها ضایعات فولاد را بازیافت میکند، بلکه امکان آلیاژسازی دقیق و سفارشیسازی را نیز فراهم میکند و نیازهای مختلف صنعت را برآورده میکند. پیشرفتها در فناوری EAF، مانند سیستمهای شارژ مداوم و اتوماسیون فرآیند، انعطافپذیری و پایداری عملیاتی را افزایش میدهند.
۵. آلیاژسازی: ویژگی های فولاد تنظیم دقیق
آلیاژسازی آهن مذاب را به فولاد با خواص مکانیکی، شیمیایی و حرارتی خاص تبدیل می کند. عناصر آلیاژی مانند کربن، منگنز، کروم و نیکل در مقادیر کنترل شده برای دستیابی به درجه های فولادی مورد نظر، از آلیاژهای ملایم تا با استحکام بالا و مقاوم در برابر خوردگی، اضافه می شوند. طراحی آلیاژی پیشرفته، که توسط مدلسازی محاسباتی و تخصص متالورژی تسهیل میشود، عملکرد فولاد را برای کاربردهای مختلف، از اجزای خودرو گرفته تا سازههای هوافضا، بهینه میکند.
۶. ریخته گری مستمر: شکل دادن به آینده فولاد
مرحله نهایی فولاد سازی شامل ریختهگری فولاد مذاب به محصولات نیمهتمام مانند بیلت، اسلب یا شکوفه است. فناوری ریختهگری پیوسته با ایجاد فرآیندهای ریختهگری مستمر و با سرعت بالا، انقلابی در تولید فولاد ایجاد کرد. نوآوریهای طراحی قالب، هم زدن الکترومغناطیسی، و نظارت بر کیفیت آنلاین، یکنواختی و کیفیت را در محصولات ریختهگری تضمین میکند و از پردازش پایین دستی و کاهش ضایعات مواد پشتیبانی میکند.
۷. ملاحظات زیست محیطی: ایجاد تعادل در پیشرفت و پایداری
فولاد سازی و تولید فولاد فرآیندهای پر انرژی هستند و آثار زیستمحیطی قابل توجهی دارند. ذینفعان صنعت به طور فزاینده ای بر کاهش انتشار گازهای گلخانه ای، حفظ منابع و اتخاذ فناوری های پاک تر متمرکز شده اند. ابتکاراتی مانند جذب و استفاده از کربن (CCU)، فولاد سازی مبتنی بر هیدروژن، و شیوههای اقتصاد دایرهای (مثلاً بازیافت ضایعات) تلاشهای پایداری را در سراسر بخش آهن و فولاد و همسو با اهداف آبوهوای جهانی هدایت میکنند.
۸. دیجیتالی سازی و اتوماسیون: فولاد سازی در صنعت ۴.۰ Era
ادغام فناوریهای دیجیتال و اتوماسیون در حال تغییر شکل عملیات فولاد سازی است. از سیستمهای پیشرفته کنترل فرآیند گرفته تا الگوریتمهای نگهداری پیشبینیکننده، راهحلهای دیجیتال کارایی، ایمنی و تصمیمگیری را در کارخانههای فولاد افزایش میدهند. تجزیه و تحلیل داده ها در زمان واقعی، همراه با هوش مصنوعی (AI) و یادگیری ماشین، پارامترهای فرآیند را بهینه می کند، زمان خرابی را به حداقل می رساند و باعث بهبود مستمر در فرآیندهای فولاد سازی می شود.
۹. روندهای جهانی و چشم اندازهای آینده
چشم انداز فولاد سازی پویا است و تحت تأثیر روندهای بازار، پیشرفت های تکنولوژیکی و چارچوب های نظارتی است. روندهای کلیدی که آینده فولاد سازی را شکل میدهند عبارتند از:
شیوه های فولاد سازی پایدار، با تمرکز بر کربن زدایی و بهره وری منابع.
ادغام منابع انرژی تجدیدپذیر، مانند هیدروژن و زیست توده، در فرآیندهای فولاد سازی.
پیشرفت در تحقیقات متالورژی، از جمله توسعه آلیاژ جدید و تکنیک های مشخصه مواد.
ابتکارات صنعتی مشترک برای به اشتراک گذاری دانش، نوآوری و توسعه مهارت ها در تولید آهن و فولاد.
نتیجه
فولاد سازی سنگ بنای تولید فولاد مدرن است و تکنیکهای قرنها را با نوآوریهای پیشرفته ترکیب میکند. از فرآوری سنگ معدن تا طراحی آلیاژ، سفر آهن از طریق کوره های بلند، کارخانه های احیای مستقیم، کوره های قوس الکتریکی و قالب های ریخته گری پیوسته، قدرت، تطبیق پذیری و پایداری صنعت فولاد را شکل می دهد. همانطور که جهان از فناوریهای سبزتر و تحول دیجیتال استقبال میکند، فولاد سازی به تکامل خود ادامه میدهد و پایهای انعطافپذیر برای زیرساختهای جهانی و رشد اقتصادی تضمین میکند.
منبع: Steel Technology
برای مشاهده دانشنامههای بیشتر در زمینه فولاد و آهن آلات کلیک کنید
برای نوشتن دیدگاه باید وارد بشوید.