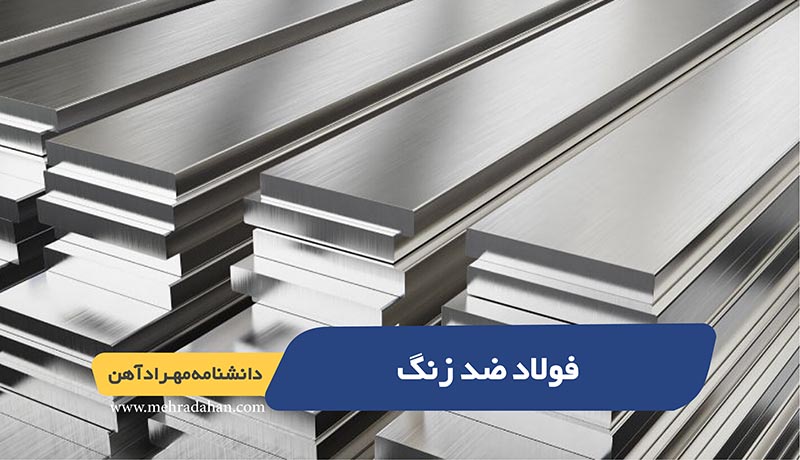
فولاد ضد زنگ
تولد فولاد به حدود ۴۰۰۰ سال قبل باز می گردد، زمانی که سلاح های آهنی به دلیل استحکام بیشتر، جای برنز را گرفتند. برای هزاران سال، اساس فولاد بدون اینکه واقعاً بدانیم چرا بهتر از جایگزین های آن است، استفاده می شد. پیشرفت های بزرگی در اواخر قرن نوزدهم و اوایل قرن بیستم رخ داد، زیرا فولاد شروع به تولیدات تجاری کرد. در سال ۱۸۵۶، هنری بسمر راه جدیدی برای کاهش محتوای کربن با وارد کردن اکسیژن به آهن مذاب ارائه کرد. این به پیشرفتهای مختلفی در فولاد منجر شد. در سال ۱۹۰۴، یک دانشمند فرانسوی به نام لئون ژیله، ترکیبی از آلیاژها را ساخت که فولاد ضد زنگ را تشکیل میداد. در سال ۱۹۱۳، هری برلی این فرآیند را مستند کرد و به مقاومت در برابر خوردگی اشاره کرد و اولین مارتنزیت را به ثبت رساند.
سایر مواد + (٪۱۰.۵>) کروم + آهن = فولاد ضد زنگ
نحوه تولید فولاد ضد زنگ
معادله بالا اساس یک آلیاژ فولاد ضد زنگ را تشکیل می دهد، اما از همه انواع عناصر برای تشکیل درجات مختلف ضد زنگ استفاده می شود. این گریدهای مختلف خواص و قابلیت های متفاوتی دارند و به همین دلیل در بسیاری از موارد برای اهداف متفاوتی استفاده می شوند. بیشتر تولید فولاد ضد زنگ در گروه ۱۰ آلیاژی است، اما در حال حاضر بیش از ۲۵۰ آلیاژ فولاد ضد زنگ وجود دارد.
فولاد ضد زنگ معمولاً حاوی ۱۰ تا ۳۰ درصد کروم می باشد. کروم در ترکیب با کربن، مقاومت قابل توجهی در برابر خوردگی و گرما ایجاد می کند. عناصر دیگری مانند نیکل، مولیبدن، تیتانیوم، آلومینیوم، نیوبیم، مس، نیتروژن، گوگرد، فسفر یا سلنیوم نیز ممکن است برای افزایش مقاومت در برابر خوردگی، افزایش مقاومت در برابر اکسیداسیون و ایجاد ویژگیهای خاص اضافه شوند. اکثر فولادهای ضد زنگ ابتدا در کوره های قوس الکتریکی یا اکسیژن پایه ذوب می شوند و متعاقباً برای کاهش محتوای کربن تصفیه می شوند. در فرآیند کربن زدایی آرگون-اکسیژن، مخلوطی از اکسیژن و گاز آرگون به فولاد مایع تزریق می شود. با تغییر نسبت اکسیژن و آرگون، می توان کربن را تا سطوح کنترل شده با اکسید کردن آن به مونوکسید کربن حذف کرد، بدون اینکه کروم گران قیمت را از دست داد. بنابراین، مواد خام ارزانتر، مانند فروکروم با کربن بالا، ممکن است در عملیات ذوب اولیه استفاده شوند.
چرا فولاد ضد زنگ در تولید بسیار محبوب است؟
چه چیزی فولاد ضد زنگ را در مقایسه با سایر فلزات عالی می کند؟ این فلز در برابر خوردگی مقاومتر است (زنگ نمیزند)، مقاومت در برابر حرارت و اکسیداسیون بالاتری نسبت به فلزات دیگر دارد و در مقایسه با سایر فلزات هم در دمای اتاق و هم در دماهای بالا استحکام بالاتری دارد. علاوه بر این ویژگی ها، ویژگی های منحصر به فرد فولاد ضد زنگ، ظاهر آن و نیاز کم آن به نگهداری بوده که همه این ویژگی ها آن را به گزینه ای قوی برای بسیاری از کاربردها تبدیل کرده است. بیایید مقاومت در برابر خوردگی را کمی بیشتر بررسی کنیم. چرا مقاومت در برابر خوردگی دارد؟ چرا فولاد ضد زنگ زنگ نمی زند؟ پاسخ کوتاه است: کروم. بیایید به معادله خود در بالا نگاه کنیم. آهن که فلز پایه در اکثر فولادهای زنگ نزن است، معمولاً در صورت قرار گرفتن در معرض اکسیژن به سرعت زنگ میزند. چیزی که فولاد ضد زنگ را از فولاد کربنی یا دیگر انواع فولاد متمایز می کند، لایه اکسید کرومی است که به این فلز پایه اضافه می شود. این لایه برای تشکیل یک لایه غیرفعال عمل می کند که مقاومت در برابر خوردگی را تا حد زیادی افزایش می دهد و به نوبه خود زنگ زدگی را به حداقل می رساند. همانطور که می توان حدس زد، افزایش مقدار کروم باعث افزایش مقاومت در برابر خوردگی می شود. فولاد ضد زنگ گزینه های آلیاژی مختلفی دارد و متالورژی متفاوت هر آلیاژ منجر به خانواده های مختلف فولاد ضد زنگ و گریدهای متفاوت در آن خانواده ها می شود.
۵ دسته اصلی در خانواده فولاد ضد زنگ وجود دارد:
۱- فولاد ضد زنگ آستنیتی (سری ۲۰۰ و ۳۰۰): متداول ترین نوع فولاد ضد زنگ، فولادهای زنگ نزن آستنیتی بوده که به دلیل مقاومت استثنایی خود در برابر حرارت و خوردگی شناخته شده اند.
۲- فولاد ضد زنگ مارتنزیتی (سری ۴۰۰ و ۵۰۰): بر خلاف فولاد آستنیتی، فولاد ضد زنگ مارتنزیتی را می توان با حرارت سخت کرد. این فرآیند فولاد مارتنزیتی را قوی تر از سایر انواع می کند.
۳- فولاد ضد زنگ فریتی (سری ۴۰۰): فولادهای فریتی حاوی بیش از ۱۲ درصد کروم هستند که اساساً با عملیات حرارتی سخت نمی شوند و فقط اندکی با نورد سرد سخت می شوند.
۴- فولاد ضد زنگ رسوب سخت شونده (درجات PH): آلیاژهای PH فولاد ضد زنگ حاوی مقدار کمی مس، آلومینیوم، فسفر یا تیتانیوم هستند. پس از اینکه یک قطعه از این آلیاژها تشکیل شد، یک عملیات سخت شدن انجام می شود که در آن این عناصر به صورت ترکیبات سخت بین فلزی رسوب می کنند که به طور قابل توجهی سختی و استحکام را افزایش می دهد.
۵- فولاد ضد زنگ داپلکس: به این نوع فولاد ضد زنگ «داپلکس» می گویند زیرا این آلیاژها دارای ریزساختار دو فازی هستند که از دانه های فولاد زنگ نزن فریتی و آستنیتی تشکیل شده است.
این دسته ها، درجه های مختلفی از ضد زنگ بودن را دارند. افزودن عناصر مختلف، ساختار شیمیایی هر گرید را تغییر میدهد و عوامل آن درجه را تغییر میدهد که میتواند بر کاربرد ماده تأثیر بگذارد. به عنوان مثال، در مورد شکل پذیری در مقابل جوش پذیری.
نقش نیکل در فولاد ضد زنگ
بیش از دو سوم تولید جهانی نیکل برای تولید فولاد ضد زنگ استفاده می شود. نیکل به عنوان یک عنصر آلیاژی، خواص مهمی مانند شکلپذیری و جوشپذیری را افزایش میدهد و در عین حال مقاومت به خوردگی را در کاربردهای خاص افزایش میدهد. فولاد ضد زنگ بیش از صد سال است که مورد استفاده قرار می گیرد. این شامل طیف گسترده ای از آلیاژهای مبتنی بر آهن است، اما بر خلاف فولاد معمولی در برابر خوردگی مقاوم هستند و هنگامی که به تنهایی در معرض آب قرار می گیرند زنگ نمی زنند. همانطور که پیشتر گفته شد، عنصر آلیاژی که فولاد را ضد زنگ می کند کروم است. با این حال، افزودن نیکل است که فولاد ضد زنگ را قادر می سازد تا به چنین آلیاژی همه کاره تبدیل شود. فولادهای ضد زنگ حاوی نیکل علاوه بر مقاومت ذاتی در برابر خوردگی، به راحتی شکل می گیرند و جوش می شوند. آنها در دماهای بسیار پایین انعطاف پذیر می مانند و در عین حال می توانند برای کاربردهای در دمای بالا استفاده شوند. علاوه بر این، بر خلاف فولاد معمولی و فولاد ضد زنگ غیر حاوی نیکل، غیر مغناطیسی هستند. این بدان معناست که آنها را می توان به طیف وسیعی از محصولات تبدیل کرد که کاربردهای گسترده ای در صنایع شیمیایی، بخش بهداشت و مصارف خانگی دارد. در واقع، نیکل آنقدر مهم است که گریدهای حاوی نیکل ۷۵ درصد از تولید فولاد ضد زنگ را تشکیل می دهند. شناخته شده ترین آنها نوع ۳۰۴ است که ۸ درصد نیکل دارد و نوع ۳۱۶ که ۱۱ درصد دارد. نیکل این خواص را با تغییر ساختار بلوری فولاد به ساختار آستنیتی (کریستال مکعبی محور) در تقریباً تمام دماها فراهم می کند. فولاد معمولی دارای ساختار فریتی (کریستال مکعبی بدنه) در دمای محیط است.
این افزودن نیکل – معمولاً ۸ تا ۱۰٪ – است که این ویژگی های منحصر به فرد را ایجاد می کند. نیکل به قدری مهم است که گریدهای حاوی نیکل ۷۵ درصد از تولید فولاد ضد زنگ را تشکیل می دهند. در نمودار زیر درصد کروم و نیکل استفاده شده در انواع فولاد ضد زنگ را نشان می دهد.
۶ ویژگی اصلی فولاد ضد زنگ حاوی نیکل
۱– شکل پذیری:
ساختار آستنیتی فولادهای ضد زنگ را با شکل پذیری خوبی فراهم می کند. ۱۸% کروم معمولی و نیکل ۸% نوع ۳۰۴ به ویژه ویژگیهای کششی خوبی را نشان میدهد. مقدار کمی نیکل بالاتر، پایداری آستنیت را بیشتر میکند و تمایل به سخت شدن کار را کاهش میدهد. برخلاف آلیاژهای کم نیکل و منگنز بالا، این آلیاژها مستعد ترک خوردگی سرد تاخیری نیستند. شکل پذیری عالی آنها باعث شده است که آلیاژهای آستنیتی سری ۳۰۰ به طور گسترده برای مواردی مانند سینک آشپزخانه و قابلمه های پخت و پز استفاده شوند.
۲– قابلیت جوشکاری:
بسیاری از تجهیزات فولاد ضد زنگ با جوشکاری ساخته می شوند. به طور کلی، آلیاژهای آستنیتی نیکل نسبت به سایر آلیاژها برای جوشکاری بهتر هستند، به طوری که سری ۳۰۴ و ۳۱۶ پرکاربردترین فولادهای ضد زنگ در جهان هستند. برخلاف آلیاژهای فریتی، آنها در دمای بالا مستعد شکنندگی نیستند و جوش ها خواص خمشی و ضربه ای عالی دارند. آنها به راحتی در هر دو بخش ضخیم و نازک قابل جوش هستند.
۳– سختی یا چقرمگی:
سختی، توانایی یک ماده برای جذب انرژی بدون شکستن است. اکثر فولادهای ضد زنگ در دمای اتاق چقرمگی خوبی دارند، با این حال، با کاهش دما، ساختار فریتی به تدریج شکننده تر می شود و فولاد ضد زنگ فریتی را برای استفاده در دماهای برودتی نامناسب می کند. در مقابل، فولادهای زنگ نزن آستنیتی معمولی حتی در دمای هلیوم مایع (۲۷۰ درجه سانتیگراد) چقرمگی خوبی را حفظ می کنند، به همین دلیل است که گریدهایی مانند نوع ۳۰۴ به طور گسترده برای کاربردهای برودتی استفاده می شوند.
۴– ویژگی دمای بالا:
افزودن نیکل به آلیاژهای آستنیتی فولاد ضد زنگ استحکام قابل توجهی در دمای بالا نسبت به سایر آلیاژها می دهد، به ویژه توانایی مقاومت در برابر تمایل به حرکت آهسته یا تغییر شکل دائمی تحت تنش های مکانیکی، معروف به خزش. این آلیاژها همچنین زمانی که در معرض دمای بیش از ۳۰۰ درجه سانتیگراد قرار می گیرند، بسیار کمتر مستعد تشکیل فازهای شکننده آسیب رسان هستند. نیکل همچنین لایه اکسید محافظ را تثبیت می کند و پوسته پوسته شدن را در طول چرخه حرارتی کاهش می دهد. به همین دلیل است که آلیاژهای آستنیتی برای کاربردهای با دمای بالا و در جاهایی که مقاومت در برابر آتش مورد نیاز است ترجیح داده می شوند.
۵– پایداری
اکثر مواد حاوی نیکل در پایان عمر مفید محصول کاملاً قابل بازیافت هستند. در واقع ارزش بالای آنها تمایل به بازیافت را زیاد می کند. این به نوبه خود، اثرات زیست محیطی فولادهای ضد زنگ حاوی نیکل را با کاهش نیاز به مواد اولیه و انرژی مورد استفاده در تولید آنها کاهش می دهد. به عنوان مثال، مقدار ضایعات فولاد ضد زنگ که در حال حاضر استفاده می شود، انرژی مورد نیاز برای تولید فولاد ضد زنگ را تا حدود یک سوم نسبت به استفاده از مواد ۱۰۰٪ بکر کاهش می دهد.
۶– سهولت در تولید
سهولت تولید چیزی نیست که بلافاصله برای کاربر نهایی آشکار شود. با این حال، تجربه طولانی در ساخت آلیاژهای آستنیتی رایج، استفاده گسترده از آنها، تطبیق پذیری و مقیاس تولید آنها باعث شده است که آنها به طور گسترده و اقتصادی در همه اشکال و مقادیر و در تمام نقاط جهان در دسترس باشند.
کدام گرید فولاد ضد زنگ برای شکلپذیری بهتر است؟
اگر کسی به دنبال آلیاژی با شکل پذیری بهتر باشد، باید به دنبال آلیاژی با محتوای نیکل، مس و منگنز افزایش یافته مانند سیم فولادی زنگ نزن ۳۰۵ باشد. کاربردهای معمولی فولاد ضد زنگ ۳۰۵ عبارتند از: تولید قطعات پزشکی و قطعات جراحی
کدام گرید فولاد ضد زنگ برای جوشکاری بهتر است؟
در حالی که به دنبال آلیاژی با قابلیت جوشکاری بهتر هستیم، میتوانیم به دنبال گزینهای با محتوای تیتانیوم یا نیوبیم افزایش یافته باشیم، مانند فولاد ضد زنگ 316L. کاربردهای معمولی فولاد ضد زنگ 316L عبارتند از: صفحه نمایش های شیمیایی، پالایشگاه های نفت، شیلنگ های فلزی انعطاف پذیر، قطعات صنعت نساجی
کدام گرید فولاد ضد زنگ استحکام بیشتری دارد؟
یکی دیگر از مشخصه های متداول که سازندگان در طول قطعه سازی به دنبال آن هستند، مواد با استحکام بیشتر است. این امر با فولاد ضد زنگ با افزودن کربن، نیتروژن و یا وانادیوم به آلیاژ ضد زنگ به دست می آید. فولاد ضد زنگ ۴۴۰ دارای محتوای کربن بالاتری نسبت به اکثر گزینه های ضد زنگ است و بنابراین یکی از آلیاژهای قوی تری است که ما در دسترس داریم. کاربردهای معمولی فولاد ضد زنگ ۴۴۰ عبارتند از: لوازم جراحی مانند چاقو و قیچی، سلاح گرم
کدام گرید فولاد ضد زنگ مقاومت اکسیداسیون بالایی دارد؟
مقاومت در برابر اکسیداسیون یکی دیگر از ویژگی های محبوبی است که قطعه سازان در نیازهای فلزی خود به دنبال آن هستند. مقاومت در برابر اکسیداسیون یک مقاومت غیر معمول است، زیرا در فولاد ضد زنگ با افزایش محتوای سیلیکون و یا آلومینیوم به دست میآید. فولاد ضد زنگ ۳۲۱ به دلایل زیادی یک انتخاب محبوب است، زیرا محتوای سیلیکون بالاتر آن باعث مقاومت بهتر در برابر اکسیداسیون می شود. کاربردهای معمولی فولاد ضد زنگ ۳۲۱ عبارتند از: قطعات اگزوز خودرو، قطعات موتور جت، اتصال دهنده ها، حلقه های جمع کننده هواپیما، لوله و …
منبع: Steel Technology
برای مشاهده دانشنامههای بیشتر در زمینه فولاد و آهن آلات کلیک کنید